POWDER COATING TROUBLESHOOTING
TYPES OF METAL SUBSTRATE
- CRCA (COLLED ROLLED CLOSE - ANNEALED)
|
|
|
|
|
- GPSP (GALVANIZED PLANE-SINGLE PASS)
|
|
|
PRETREATMENT (TO CLEAN THE METAL SUBSTRATE)
- PHOSPHATING (FOR CRCA, HR)
|
- CHROMOTIZING (FOR ALUMINIUM)
|
- SHOT BLASTING (FOR HIGH-THICKNESS MATERIAL)
|
- SANDING (FOR HIGH-THICKNESS MATERIAL)
|
PHOSPHATING 7 TANK HOT PROCESS
COLD PROCESS (3 IN ONE)
7 TANK PROCESS WITH CHECK POINT
1. DEGREASING : CLEANING THE SHEET METAL SURFACE GREASE, OILS,SOILS,LUBRICANTS, OXIDE FILMS.
- CHEMICAL : ALKALINE DEGREASER
- TEMPERATURE : 60°C9±10°C
- POINTAGE : AS PER CHEMICAL SUPPLIER
- DURATION : 10-15 MINUTES
2. WATER RESIGNING: CLEANING THE SHEET METAL SURFACE GREASE, OILS, SOILS, LUBRICANTS, OXIDE FILMS.
- TEMPERATURE : AMBIENT ROOM TEMPERATURE
- DURATION : 5 MINUTES
3. DE-RUSTING: CLEANING THE SHEET METAL SURFACE OF RUST.
- CHEMICAL : RUST REMOVER
- TEMPERATURE : AMBIENT ROOM TEMPERATURE
- POINTAGE : AS PER CHEMICAL SUPPLIER
- DURATION : 10 MINUTES
4. DM WATER RESIGNING: CLEANING THE SHEET METAL SURFACE OF RUST.
- TEMPERATURE : AMBIENT ROOM TEMPERATURE
- DURATION : 5 MINUTES
- PH VALUE : 5 TO 7
5. SURFACE ACTIVATION : SURFACE ACTIVATION FOR PHOSPHATING LAYER
- CHEMICAL : ACTIVATOR (AS PER CHEMICAL SUPPLIER )
- TEMPERATURE : AMBIENT ROOM TEMPERATURE
- DURATION : 5-10 MINUTES
6. PHOSPHATING
- CHEMICAL : ZINC OR IRON PHOSPHATE
- TEMPERATURE : 40°C+-10°C
- POINTAGE : AS PER CHEMICAL SUPPLIER
- DURATION : 5-10 MINUTES(ACCORDING JOB)
7. DM WATER RESIGNING
- TEMPERATURE : AMBIENT ROOM TEMPERATURE
- DURATION : 5 MINUTES
- PH VALUE : 5 TO 7
CHROMOTIZING PROCESS
NON-CHROMOTIZING PROCESS
CHROMATING PROCESS WITH CHECK POINTS
1. DEGREASING : CLEANING THE ALUMINUM SURFACE OF GREASE, OILS, SOILS AND LUBRICANTS FILMS.
- CHEMICAL : ACID DEGREASER
- TEMPERATURE : AMBIENT ROOM TEMPERATURE
- POINTAGE : AS PER CHEMICAL SUPPLIER
- DURATION : 10-15 MINUTES
2. DM WATER RESIGNING
- TEMPERATURE : AMBIENT ROOM TEMPERATURE
- DURATION : 5-7 MINUTES
- PH VALUE : 5 TO 7
3. ETCHING : THE PURPOSE OF ETCHING PROCESS IS TO REMOVE THE THIN NATURAL OXIDE LAYER ON THE SURFACE BEFORE THE CHROMATING.
- TEMPERATURE : AMBIENT ROOM TEMPERATURE
- POINTAGE : AS PER CHEMICAL SUPPLIER
- DURATION : 5 MINUTES
4. DM WATER RESIGNING
- TEMPERATURE : AMBIENT ROOM TEMPERATURE
- DURATION : 5 MINUTES
- PH VALUE : 5 TO 7
5. CHROMATING
- CHEMICAL : YELLOW & GREEN CHROME
- TEMPERATURE : AMBIENT ROOM TEMPERATURE
- DURATION : 5 MINUTES
- PH VALUE : 4 TO 5
6. DM WATER RESIGNING
- TEMPERATURE : AMBIENT ROOM TEMPERATURE
- DURATION : 5 MINUTES
- PH VALUE : 5 TO 7
SUBSTRATE DRYING
- AIR
- OVEN (TEMPERATURE 100 TO 120?C)
GUN BOOTH APPLICATION (MANUALLY & AUTOMATIC)
TYPES OF GUN:-
- CORONA (MOSTLY THIS GUN USED)
- TRIBO (FOR INTRICATES
SHAPES)
TYPES OF OVENS (BATCH TYPE & CONVERISED)
- GAS FIRED
- DIESEL FIRED
- ELECTRIC FIRED
- BIO-FUEL FIRED
PROBLEMS & SOLUTIONS
CLASSIFICATION OF PROBLEMS
POWDER RELATED
APPLICATION RELATED
- FLUIDIZATION
- GUN SPITTING
- COVERING
- FILM THICKNESS
- RECYCLE POWDER
FINISH RELATED
- GLOSS
- FINISH
- COLOR CHANGE
- PIN HOLES
- ORANGE PEEL
MECHANICAL & CHEMICAL TEST
- IMPACT TEST
- BAND TEST
- CROSS HATCH TEST
- SST TEST
- QUV TEST
LUMPS FORMATION
POSSIBLE CAUSE
|
SUGGESTED SOLUTION
|
- THE POWDER HAS BEEN STORE FOR TOO LONGER TIME OR TEMP TOO HIGH FOR
STORAGE
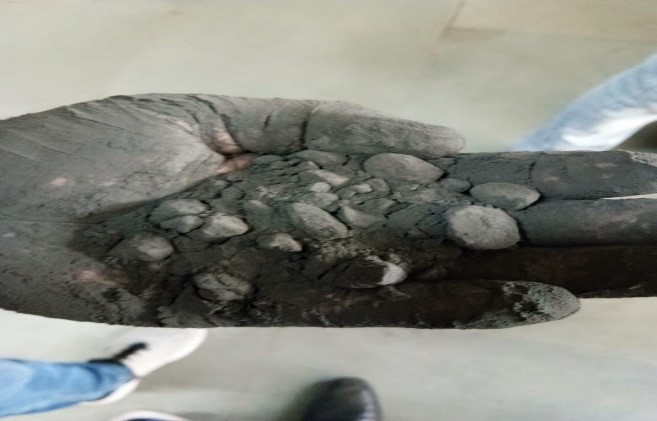
|
- KEEP POWDER COOL & DRY AREA.
- FILTER THE POWDER
|
GUN SPITTING
POSSIBLE CAUSE
|
SUGGESTED SOLUTION
|
-
POOR FLUIDIZATION IN POWDER HOPPER PUMP & BLOCKED HOSES NOT ADJUSTED PROPERLY
- PUMP & BLOCKED HOSES NOT ADJUSTED PROPERLY
|
- INCREASE OR DECREASE THE FLUIDIZING AIR TO HOPPER
- CHECK BOTTOM OF HOPPER AND MEMBRANE FILTER
- INCREASE ATOMIZING/ DIFFUSER AIR
- CHECK ALL AIR TUBE CONNECTIONS FOR LEAK
- REDUCE THE AMOUNT OF RECLAIM POWDER
|
POOR PENETRATION (COVERING)
POSSIBLE CAUSE
|
SUGGESTED SOLUTION
|
- INSUFFICIENT POWDER
- POOR EARTH
- INCORRECT SPRAY PATTERN
- VOLTAGE TOO FINE
- POWDER TOO FINE
|
- INCREASE THE PUMP FLOW-RATE PRESSURE
- CLEAN THE HOOK AND RACKS, ALSO CHECK AND IMPROVED GROUNDING
- TRY DIFFERENT NOZZLES FOR DIFFERENT SURFACE
- REDUCE GUN VOLTAGE (Kv)
- REDUCE THE AMOUNT OF RECLAIM POWDER
|
COVERAGE
POSSIBLE CAUSE
|
SUGGESTED SOLUTION
|
- POWDER DELIVERY RATE TO HIGH (EFFECT-THICKNESS)
- SHAPE OF SUBSTRATE
- INCORRECT SPRAY COATING METHOD
- RECYCLE POWDER EFFICIENCY
- POOR EARTH
|
- POWDER DELIVERY RATE DECREASED (CONTROL-THICKNESS)
- DIFFERENT SHAPE CHANGE AREA
- CHECK GUN DISTANCE & COATING METHOD
- CHECK RECYCLE POWDER %
- CLEAN HOCKS , HANGER & IMPROVED GROUNDING
|
GUN PARAMETERS FOR POWDER
FINISH
|
SMOOTH
|
STRUCTURE
|
TEXTURE
|
METALLIC
|
CHARGING (Kv)
|
70-90
|
70-100
|
70-80
|
50-60
|
AIR (Kg/Cm3)
|
1.5-4.0
|
1.0-2.5
|
1.5-4.0
|
0.5-1.5
|
POWDER
|
As Per Required
|
As Per Required
|
As Per Required
|
As Per Required
|
CURRENT(????A)
|
20-40
|
20-40
|
20-40
|
20-30
|
FLUIDIZATION(Kg/Cm3)
|
As Per Required
|
As Per Required
|
As Per Required
|
As Per Required
|
FILM THICKNESS TOO LOW OR TOO HIGH
POSSIBLE CAUSE
|
SUGGESTED SOLUTION
|
- POWDER DELIVERY TOO LOW
- INSUFFICIENT COATING TIME
- FARADAY CAGE EFFECT
- POOR EARTHING
- POWDER OUTPUT TOO HIGH
|
- INCREASES COATING TIME OF COMPONENT
- ADJUST THE GUN VOLTAGE & OTHER PARAMETERS
- CLEAN HOOKS & RACKS
- TURN DOWN PUMP PRESSURE & MOVE GUN FARTHER AWAY FROM THE PARTS REDUCE GUN VOLTAGE
- REDUCE TIME OF COMPONENT COATING TIME
|
CRATERS & PIN HOLES
POSSIBLE CAUSE
|
SUGGESTED SOLUTION
|
- OIL & OTHER CONTAMINATION ON PARTS
- CONTAMINATED COMPRESSED AIR
- CONTAMINATED POWDER
- MOISTURE IN AIR
- SILICON CONTAMINATION
- POOR SHEET QUALITY
|
- CHECK CLEANING AND PRETREATMENT
- ENSURE COMPRESSED AIR IS FREE FROM OIL
- CLEAN THE EQUIPMENT AND RECHARGE WITH FRESH POWDER
- DRAIN OUT THE WATER FROM COMPRESSOR
- REMOVE LOCATED SOURCE POINT
- CHOOSE SPECIAL DEGASSING GRADE POWDER MICRO PINHOLE IN GPSP SHEET
|
GLOSS (TOO HIGH OR TOO LOW)
POSSIBLE CAUSE
|
SUGGESTED SOLUTION
|
- CURE OVEN TEMP TOO LOW
- CURE OVEN TEMP TOO HIGH
- OVEN CYCLE TIME LOW & LONG
- CONTAMINATION WITH INCOMPATIBLE POWDER
|
- INCREASE THE OVEN TEMP
- DECREASE THE OVEN TEMP
- ADJUST LINE SPEED & CURING TIME
- REMOVE ALL CONTAMINATED POWDER THOROUGHLY CLEAN ALL EQUIPMENT THEN USE FRESH POWDER
|
POOR ADHESION (CHIP-OFF)
POSSIBLE CAUSE
|
SUGGESTED SOLUTION
|
- POWDER UNDER CURE
- POOR PRETREATMENT (OIL & DIRTY SURFACE)
- HIGH COATING
- PREHEAT AFTER PRE-TREATMENT PROCESS
|
- INCREASE THE TEMP
- CHECK THE PRETREATMENT PROCESS
- ADJUST COATING AS PER PRODUCT STD
- CHECK CONDITION & SUGGESTED FOR PREHEAT
|
COLOR VARIATION
POSSIBLE CAUSE
|
SUGGESTED SOLUTION
|
- FILM THICKNESS VARIATION
- DIFFERING SUBSTRATES & SUBSTRATE COLOR
- OVER CURING OF POWDER COATING
|
- ASSURE CONSTANT FILM THICKNESS
- USE SUBSTRATE OF SAME TYPE FOR COMPARISONS
- OBSERVE CURING PARAMETERS OF POWDER MANUFACTURER
|
COLOR FADING
POSSIBLE CAUSE
|
SUGGESTED SOLUTION
|
- CLEANING METHOD VERY POOR
- POOR PAINT FILM ADHESION
- SMALL PIN HOLE & DEGASSING ON FINISH
- SUN UV RAYS, MANY POLLUTANT SECTION ARE FASTER FADE SOME PLACE
- CHOOSE WRONG CHEMISTRY POWDER
- COLOR HAS A LIMITED LIFE EXPECTANCY
|
- CHECK PRE-TREATMENT PROCESS
- CHECK TEMPERATURE
- CHEEK PINHOLE SOURCE
- DISCUSS CONDITIONS WITH MANUFACTURE
- CHOOSE OUTDOOR DURABILITY ARCHITECTURAL GRADE POWDER
- CONTACT MANUFACTURE
|
STRUCTURE PATTERN
POSSIBLE CAUSE
|
SUGGESTED SOLUTION
|
- FLAT PATTERN
- SMALL PATTERN (PIN HOLE)
|
- ADJUST THE AIR PRESSURE & LOWER THICKNESS
- INCREASE THICKNESS. LONG CURING TIME
|
DUSTING (FOREIGN PARTICLE IN FILM)
POSSIBLE CAUSE
|
SUGGESTED SOLUTION
|
- SUBSTRATE SURFACE IS DIRTY
- BOOTH AREA IS NOT CLEAN
- POWDER IS TOO COARSE OR NOT SIEVED
|
- CHECK THE PRETREATMENT PROCESS
- CLEAN THE SUBSTRATE BY AIR CLEANING
- CLEAN THE BOOTH AREA. SIEVE ALL RECLAIM POWDER
|
ORANGE PEEL (POOR FLOW)
POSSIBLE CAUSE
|
SUGGESTED SOLUTION
|
- FILM THICKNESS IS TOO HIGH OR TOO LOW
- VOLTAGE TOO HIGH
- HEAT CYCLE OF THE TOO SLOW
- AIR PRESSURE IS TOO HIGH
|
- CHECK SYSTEM PARAMETERS
- OPTIMIZE VOLTAGE
- DETERMINE THE HEAT UP CURVE AND INCREASE
- REDUCE THE AIR PRESSURE
|
CLOUD PROBLEM (CARBON LAYER) IN FINISH
POSSIBLE CAUSE
|
SUGGESTED SOLUTION
|
- CORROSIVE URBAN ATMOSPHERE
- UNIFORM EXPOSURE TO AIR & ITS POLLUTANTS
- COATING DEFECTS OR COATING DAMAGE
- UNCURED SUBSTRATE
- CHLORIDE CONTAMINATION ON PHOSPHATE FILM
- DAMP MOISTURE FILMS OVER METAL SURFACE
- WET FILMS OF DEW & RAINWATER
|
- USE CORROSION RESISTANT METAL OR ALLOY
- REDUCE ATMOSPHERIC POLLUTANTS
- DO REGULAR SURFACE CLEANING
- CHECK CURING TEMPERATURE REGULARLY
- AVOID COATING DEFECTS
- USE SUITABLE CORROSION INHIBITORS
- COATED SUBSTRATE PACKING AREA SHOULD BE DRY
|
CORROSION (RUST)
POSSIBLE CAUSE
|
SUGGESTED SOLUTION
|
- CORROSIVE URBAN ATMOSPHERE
- UNIFORM EXPOSURE TO AIR & ITS POLLUTANTS
- COATING DEFECTS OR COATING DAMAGE
- UNCURED SUBSTRATE
- CHLORIDE CONTAMINATION ON PHOSPHATE FILM
- DAMP MOISTURE FILMS OVER METAL SURFACE
- WET FILMS OF DEW & RAIN WATER
|
- USE CORROSION RESISTANT METAL OR ALLOY
- REDUCE ATMOSPHERIC POLLUTANTS
- DO REGULAR SURFACE CLEANING
- CHECK CURING TEMPERATURE REGULARLY
- AVOID COATING DEFECTS
- USE SUITABLE CORROSION INHIBITORS
- COATED SUBSTRATE PACKING AREA SHOULD BE DRY
|
USE OF RECYCLE POWDER
- MAINTAIN USE OF RECYCLE POWDER PERCENTAGE WITH MAXIMUM (70:30) RATIO. IF WE USE WITH HIGHER RATIO THAT CAUSE PROBLEM IN FINISH.
- USE RECYCLE POWDER ONLY AFTER SIEVING. IF WE USE WITHOUT SIEVING THAT CAUSE DUSTING.
- COLLECT THE RECYCLE POWDER SEPARATE BOX & COVER PROPERLY OTHERWISE FACE IN PINHOLE PROBLEM.
COLOR VARIATION (IN METALLIC)
POSSIBLE CAUSE
|
SUGGESTED SOLUTION
|
- HIGH CHARGING
- HIGH AIR PRESSURE
- GUN DISTANCE TOO HIGH OR TOO LOW
- COLOR VARIATION IN RECYCLING
|
- REDUCE THE CHARGING TO BELOW 60 KV
- OPTIMIZE THE AIR PRESSURE
- ADJUST THE GUN DISTANCE
- MAINTAIN 90/10 RATIO USE OF RECYCLE POWDER
|
TTR (TRAVELLING TEMPERATURE RECORDER)
-
DATA LOGGER : TTR data logger is a portable measuring
device that is capable of autonomously recording temperature over a
defined period of time. The digital data can be retrieved, viewed and evaluated
after it has been recorded.
- PROBE : The type K is the
most common type of thermocouple.
- INSULATION BOX : It insulate heat to protect data logger.
TTR GRAPH RESULT NOT OK
TTR GRAPH RESULT OK
TTR RESULTS (CONVEYOR OVEN)